There are several ways of producing hydrogen and the ACO has naturally opted for ‘green’ hydrogen, i.e. that produced using a carbon-free process.
- ‘Green’ hydrogen can come from the fermenting of bioresources such as biomass, waste or methane.
- ‘Green’ hydrogen can be obtained using water electrolysis where the electricity is generated by renewable sources (water electrolysis applies an electrical current to split water into oxygen and hydrogen).
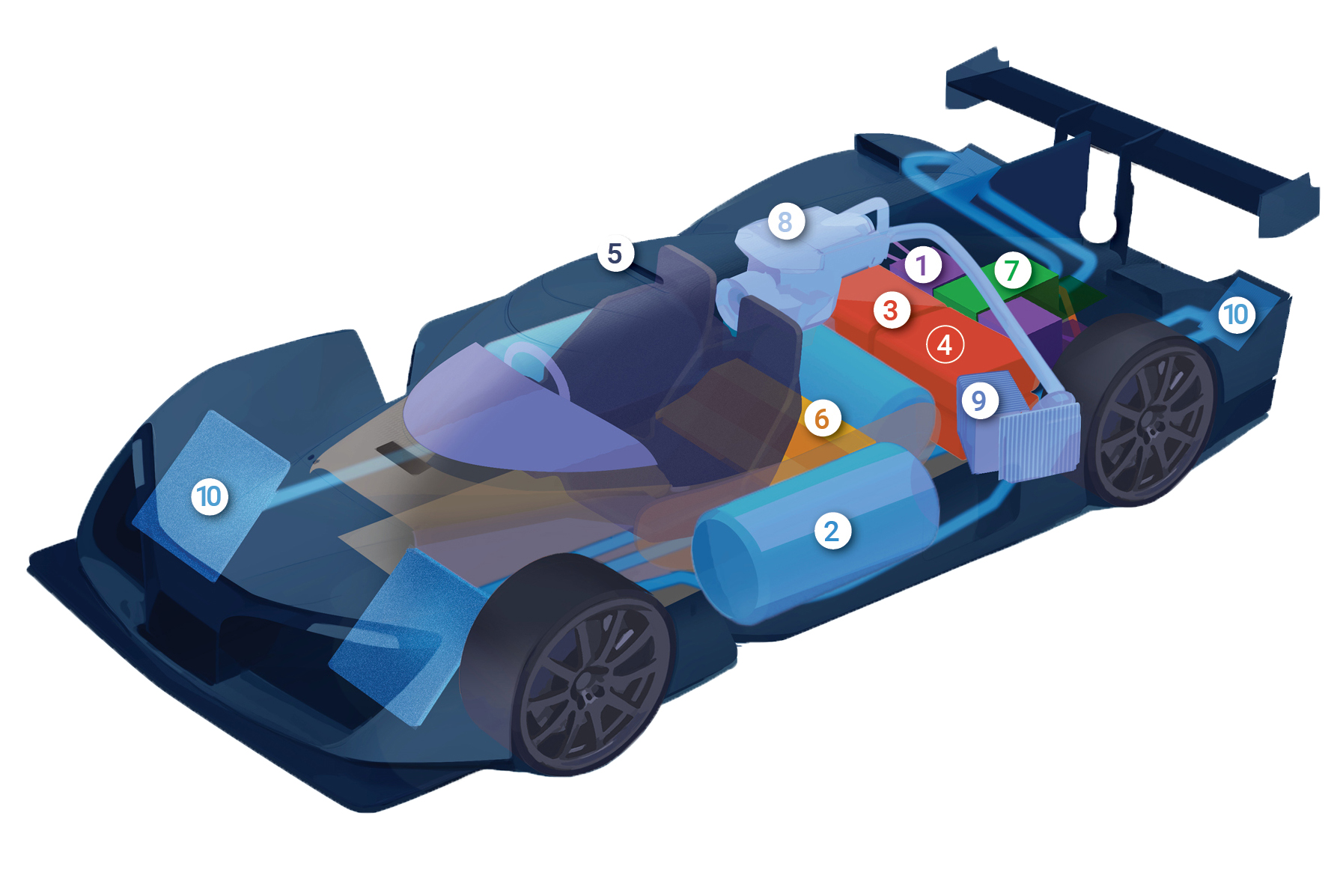
1.Electric motors: Four electric motors on the rear wheels (two on each) provide propulsion.
2.Three hydrogen reservoirs: The dihydrogen (H2) is stored in three pressurized (700 bars) carbon filament tanks used to fuel the cell. The first two are placed either side of the cockpit and the third just behind the driver.
3.Hydrogen fuel-cell: Comprises four stacks, at the core of which molecules of dihydrogen (H2, stored in the tanks) and oxygen atoms combine to form water molecules (H2O). This reaction produces heat, and electricity, which powers the car’s electric motor.
4.The stack A layered pile of 230 cells, bipolar plates and hydrogen porous membranes.
5.Air Intake: The ambient air used to produce the reaction within the stacks enters through this vent. It is filtered, propelled towards the compressor, then the humidifier, before entering the stacks.
6.Buffer batteries: Excess electricity produced by the hydrogen fuel-cell and by the KERS system (when braking) feeds into high-performance cells. The driver can therefore double the car’s acceleration potential (250–480 kw, the equivalent of 653 hp).
7.Transmission : A special, clutchless one-gear gear box manages rear wheels independently and is designed to reduce grinding.
8.Compressor: Compresses and accelerates the air that enters via the vent (up to 300g per second). It operates at up to 100000 revolutions per minute. The modulation of the air flow injected in the stacks alters the reaction and therefore determines the amount of electric power produced.
9.Humidifier: Humidified air improves the interaction between oxygen atoms and dihydrogen molecules. The humidifier ensures the level of humidity of the air injected in the stacks remains constant.
10.Radiators and cooling system
11.Exhaust: The only emission produced by the GreenGT LMPH2G is water (H2O). Steam escapes through four vents (one per stack) to the rear of the car, in the middle of the aerodynamic diffuser
LMPH2G TECHNICAL DATA
Chassis:
• Carbon LMP Chassis with steel frame
• double wishbone pushrod suspension
• carbon brakes Engine:
• GreenGT electric-hydrogen powertrain (4-stack fuel cell with polymer electrolyte membrane) producing a constant 250kW
• 4 electric motors (2 per rear wheel)
• Maximum output of 480 kW at 13000 revs (653 hp)
• 2.4kWh KERS delivering 250 kW for 20 seconds
Transmission:
• Direct drive to rear wheels (ratio: 1:6.3)
• No gear box, no clutch, no mechanical differential • Electronic torque management system
Hydrogen Storage:
• Fuel tank capacity: 8.6kg of hydrogen
• Storage pressure: 700 bars Kinetic energy recovery system (KERS):
• 750V battery, nominal voltage
• Capacity: 2.4 kWh
Measurements:
• Length: 4 710 mm • Height: 1 070 mm
• Width: 1 970 mm • Wheelbase: 2 970 mm
• Front overhang: 1 000 mm
• Rear overhang: 740 mm • Weight: 1 420 kg in working order (front: 39,8 % - rear: 60,2 %)
• Weight variation at refuel: 8.6kg Wheels:
• Front 30/68-18 Michelin Pilot Sport GT (hub 12X18)
• Rear 31/71-18 Michelin Pilot Sport GT (hub 13X18) Performance:
• Maximum speed: + 300 kph • 0–100 kph: 3.4 seconds
• 400 metres, standing start: 11 seconds
• Range: equivalent to other racing cars with comparable performance
• Refuelling time: 3 minutes.
Emissions into the atmosphere:
• Water vapour only